Value engineering (VE) is a critical methodology in the construction industry, designed to enhance a project’s functionality, efficiency, and quality while reducing costs. By systematically analyzing project components, materials, and processes, VE promotes innovation, eliminates inefficiencies, and ensures optimal resource allocation. Unlike cost-cutting measures that can compromise project quality, VE focuses on achieving the best value for money while meeting or exceeding project objectives.
This article explores the principles, benefits, challenges, and best practices of value engineering in construction projects. Additionally, it examines how VE integrates into the Front-End Loading (FEL) process, ensuring maximum impact from concept to execution. This article also includes real-world case studies and practical insights to illustrate the effectiveness of VE in various construction scenarios.
What Is Value Engineering?
Value engineering is a structured, systematic approach to improving a project’s value by analyzing its functions and identifying cost-effective alternatives. The core principle of VE is that every project element serves a purpose, and by understanding that purpose, teams can identify better ways to achieve the same or improved functionality at a lower cost.
Function Over Cost
The primary goal of VE is to ensure that every component of a project serves its intended function efficiently and effectively, without unnecessary expenditures. Rather than simply reducing costs, the focus is on achieving the highest possible value by analyzing essential project functions and identifying alternative approaches that provide the same or improved results at a lower cost. For example, instead of using a high-end name brand component, an available alternative that meets the same durability and performance criteria may be chosen, reducing costs without compromising quality.
Creativity
Innovation is at the heart of value engineering. Encouraging creative problem-solving allows teams to explore alternative designs, materials, and construction methods that may provide better value. A structured brainstorming process is often used to generate and evaluate multiple solutions. This principle requires an open mindset and willingness to challenge conventional practices. A practical example is the use of 3D printing for custom-built construction components, reducing material waste and fabrication time compared to traditional methods.
Collaboration
Value engineering is most effective when multiple disciplines work together. By involving a cross-functional team, including owners, designers, engineers, contractors, and suppliers, different perspectives contribute to well-rounded, value-driven solutions. Collaboration ensures that all stakeholders’ expertise and insights are leveraged to make informed decisions. An example of this in practice is an early-stage VE workshop, where input from construction teams helps optimize the design for constructability, leading to significant cost savings and schedule improvements.
Life Cycle Perspective
Instead of only considering upfront costs, VE evaluates the total cost of ownership, including operational expenses, maintenance, and long-term performance. A cheaper initial option may lead to higher long-term costs due to increased maintenance, energy consumption, or shorter lifespan. A life cycle cost analysis (LCCA) helps compare alternatives and select the most cost-effective option over the entire life of the asset. For instance, while LED lighting systems have a higher upfront cost than traditional bulbs, they provide significant savings in energy costs and maintenance over time.
Systematic Approach
Value engineering follows a structured process, ensuring that recommendations are not based on arbitrary cost-cutting but on methodical function analysis. The process typically includes information gathering, function analysis, idea generation, evaluation, development, and implementation. This structured approach ensures a comprehensive assessment of alternatives before making changes. A practical application is the function analysis system technique (FAST), which visually maps out project functions and their relationships, aiding teams in identifying areas for improvement.
Risk Assessment
Every design decision carries some level of risk. Value engineering carefully considers potential risks associated with alternative solutions, including structural integrity, durability, regulatory compliance, and safety concerns. The goal is to identify cost-saving opportunities while ensuring that risks are minimized or mitigated through proper planning and design modifications. For example, switching to a cheaper material without verifying its long-term performance might lead to structural failures, legal liabilities, or increased maintenance costs. Therefore, thorough testing, pilot applications, and contingency planning are integral to VE implementation.

What Value Engineering Is Not
Value engineering is often misunderstood as a cost-cutting measure that sacrifices quality, but this is a misconception. VE is not about reducing costs at the expense of durability, safety, or performance. Instead, it is a strategic approach that seeks to maximize value by enhancing efficiency, improving design, and optimizing resources. The primary goal is to achieve the best possible outcome by evaluating alternatives that maintain or enhance functionality while reducing unnecessary expenses.
Common Misconceptions and Realities of Value Engineering:
Misconception: VE is a method to slash budgets and remove features.
Reality: VE identifies cost-effective alternatives that maintain or improve project objectives.
Misconception: VE leads to lower-quality materials and construction.
Reality: The process ensures that alternatives provide equal or better performance at a lower cost.
Misconception: VE is only useful for budget-constrained projects.
Reality: VE benefits all projects, regardless of budget, by improving efficiency, sustainability, and long-term performance.
The Importance of Value Engineering in Construction
Cost Optimization
Value engineering identifies and eliminates unnecessary costs while preserving or improving functionality. Through systematic analysis, VE uncovers cost-saving opportunities that may not be apparent in traditional planning.
Example: Replacing on-site poured concrete with precast elements can reduce labor costs and improve construction timelines while maintaining structural integrity.
Case Study: In a major infrastructure project, VE resulted in a 15% reduction in costs by optimizing material selection and eliminating redundant processes.
Industry Insight: A study by the Construction Industry Institute (CII) found that projects that implemented VE from the early planning stages achieved up to 30% cost savings compared to projects without VE.
Enhancing Efficiency
VE streamlines workflows, eliminates redundancies, and optimizes project schedules, ensuring that resources, whether labor, materials, or equipment, are used effectively.
Example: Modular construction techniques can reduce on-site labor requirements and accelerate project timelines.
Industry Trend: Many large-scale projects now incorporate Building Information Modeling (BIM) with VE to enhance decision-making and efficiency.
Case Study: A compressor construction project used VE to reduce construction time by 20% through prefabrication and modular design strategies.
Maintaining or Improving Quality
Contrary to the misconception that VE compromises quality, it often enhances project outcomes. By analyzing materials and methods, teams can ensure every component meets or exceeds performance standards.
Example: Replacing traditional roofing materials with high-performance thermoplastic membranes improves durability while reducing installation costs.
Insight: Studies show that VE improves long-term performance and reliability in critical infrastructure projects.
Supporting Sustainability
Value engineering promotes sustainability by encouraging environmentally friendly materials and processes. By considering life cycle costs, VE fosters energy efficiency and waste reduction.
Example: Using recycled steel instead of virgin steel reduces environmental impact without sacrificing structural performance.
Case Study: A green building project achieved LEED certification through strategic VE applications, including optimized insulation and energy-efficient HVAC systems.
Industry Best Practice: Incorporating sustainable design principles such as passive cooling, renewable materials, and energy-efficient systems in the VE process.
Facilitating Stakeholder Collaboration
VE fosters collaboration among stakeholders, ensuring that decisions align with project goals and priorities. This helps bridge gaps between owners, designers, and contractors.
Example: A VE workshop involving all stakeholders may identify cost-saving opportunities that a single team might overlook.
Practical Application: Many projects use VE reviews at major milestones to align stakeholders on cost-effective solutions.
Advanced Approach: The use of digital collaboration platforms to enhance real-time VE decision-making among globally distributed teams.
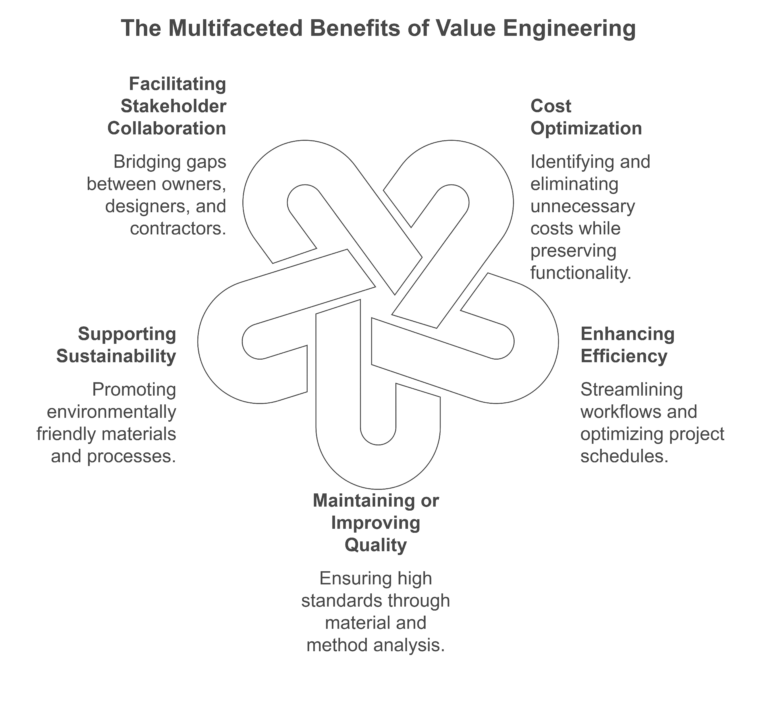
The Value Engineering Process
Value engineering is most effective when applied during the design phase but can also be used at other stages of the project lifecycle. The VE process typically includes the following steps:
1. Information Gathering
- Collect detailed project information, including objectives, design specifications, and budget constraints.
- Identify primary and secondary functions of each component.
- Perform benchmarking with industry standards and similar past projects.
- Engage key stakeholders early to align VE goals with project objectives.
2. Function Analysis
- Break down each component into its core functions and evaluate how effectively it serves those functions.
- Utilize function analysis system techniques (FAST) to visualize functional relationships.
- Identify opportunities for improvement by assessing the necessity of each function.
- Consider integrating digital modeling tools to enhance accuracy in function mapping.
3. Idea Generation
- Brainstorm alternative methods, materials, or designs to achieve the required functions more efficiently.
- Use value stream mapping to identify waste and inefficiencies.
- Facilitate cross-functional workshops to encourage diverse perspectives.
- Consider emerging technologies such as prefabrication, automation, and alternative materials.
4. Evaluation
At this stage, teams assess the feasibility, cost impact, and quality implications of proposed alternatives. The Value Engineering Log provides a structured approach to evaluating real-world alternatives, showcasing potential cost savings and improvements. The table below provides examples of key VE opportunities, with each component analyzed for better efficiency, cost reduction, and performance optimization.
Date | Project Name | Component Analyzed | Current Solution | Proposed Alternative | Expected Cost Savings (%) | Impact on Quality | Implementation Status |
2025-01-31 | Gas Processing Facility Upgrade | Heat Exchangers | Shell and Tube Exchangers | Plate Heat Exchangers | 20 | Improved Heat Transfer Efficiency | Under Review |
2025-02-05 | Pipeline Expansion | Pipeline Material | Carbon Steel Pipes | Corrosion-Resistant Alloy Pipes | 15 | Enhanced Corrosion Resistance | Approved |
2025-02-10 | Compressor Station Optimization | Compressor System | Standard Gas Compressors | Energy-Efficient Turbo Compressors | 18 | Lower Energy Consumption & Higher Efficiency | Implemented |
2025-02-15 | Storage Tank Efficiency | Storage Tank Insulation | Fiberglass Insulation | Vacuum-Insulated Panels | 22 | Better Thermal Insulation & Longevity | Pending Evaluation |
By using a structured Value Engineering Log, decision-makers can systematically evaluate each alternative’s feasibility and ensure that cost reductions align with quality, safety, and performance expectations.
- Conduct life cycle cost analysis (LCCA) for each alternative.
- Perform risk assessments to ensure proposed solutions maintain safety and compliance.
- Use decision matrices to objectively compare options based on multiple evaluation criteria.
5. Development
- Refine the best alternatives and develop detailed proposals, including cost-benefit analyses, technical specifications, and implementation plans.
- Develop prototypes or pilot studies to validate the effectiveness of proposed changes.
- Engage contractors and suppliers to ensure practical feasibility and cost-effectiveness.
6. Implementation
- Integrate selected alternatives into the project design or execution plan.
- Establish performance tracking mechanisms to ensure that VE solutions deliver expected benefits.
- Develop documentation and training for project teams to ensure smooth adoption of VE solutions.
- Monitor post-implementation performance and conduct follow-up assessments to refine VE practices.
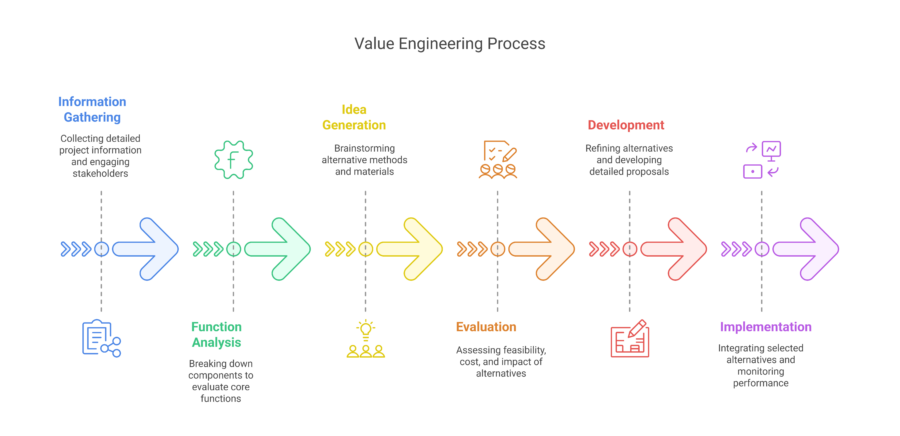
Integration of Value Engineering into the FEL Process
The Front-End Loading (FEL) process, also known as Front-End Engineering Design (FEED), is a structured approach to project planning and development. It consists of three stages: FEL-1 (Conceptual Design), FEL-2 (Preliminary Design), and FEL-3/FEED (Detailed Design and Planning). Value engineering aligns seamlessly with these phases to ensure cost optimization and functional value at every stage.
FEL-1: Conceptual Design
- Define project scope and explore cost-effective alternatives.
- Identify key cost drivers and major risks early to guide design decisions.
- Engage stakeholders, including project owners, engineers, and contractors, to gather insights and align objectives.
- Conduct feasibility studies and preliminary cost-benefit analyses to evaluate potential value-enhancing solutions.
- Explore alternative construction methodologies, such as modular construction, to reduce costs and schedule risks.
FEL-2: Preliminary Design
- Refine concepts and evaluate material and system alternatives based on life cycle costs.
- Conduct detailed function analysis to assess each component’s necessity and potential for cost reduction.
- Compare multiple design options, considering performance, sustainability, and regulatory compliance.
- Develop preliminary engineering drawings with VE recommendations incorporated.
- Perform risk assessment and mitigation strategies to ensure VE proposals do not introduce unintended vulnerabilities.
FEL-3: Detailed Design and Planning
- Finalize designs and validate VE decisions for execution.
- Conduct final cost analysis and establish implementation strategies for VE solutions.
- Optimize construction sequencing and procurement strategies to reduce delays and improve efficiency.
- Implement digital tools, such as Building Information Modeling (BIM), to simulate design alternatives and assess long-term performance impacts.
- Collaborate with suppliers and contractors to ensure cost-effective material sourcing and execution methods.
- Establish monitoring and evaluation frameworks to track the impact of VE decisions throughout the project lifecycle.
By integrating VE into the FEL process at each stage, projects can maximize value, enhance efficiency, and ensure that cost savings are achieved without sacrificing quality, safety, or performance.
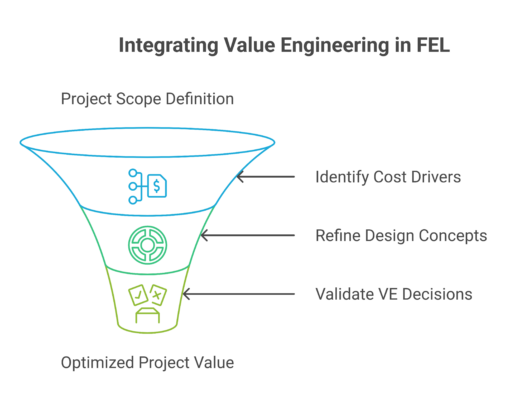
Challenges in Value Engineering
- Resistance to Change – Many stakeholders are accustomed to traditional construction methods and may hesitate to adopt new approaches introduced through VE. This reluctance is often due to a lack of understanding of the long-term benefits or fear of potential risks associated with alternative solutions. Overcoming this resistance requires effective communication, stakeholder engagement, and demonstrating proven successes of VE implementation in similar projects.
- Time Constraints – Fast-track projects with compressed schedules often struggle to incorporate a thorough VE process. Proper VE analysis requires time for information gathering, brainstorming, and evaluation, which may conflict with project deadlines. To address this challenge, project teams can integrate VE in parallel with design phases and utilize digital tools like Building Information Modeling (BIM) to accelerate the assessment of alternatives.
- Perceived Quality Risks – Some project participants associate cost-saving initiatives with reduced quality, assuming that lower-cost alternatives equate to inferior performance. This misconception can be mitigated by focusing on function-based evaluations and life cycle cost analysis (LCCA) to ensure that proposed alternatives maintain or even enhance project quality, durability, and safety.
- Data Limitations – The effectiveness of VE depends on access to accurate and up-to-date project information. Incomplete or outdated data regarding material costs, labor rates, and project requirements can lead to suboptimal decisions. Implementing robust data management systems and ensuring timely updates to cost databases and design specifications can help mitigate this issue.
Best Practices for Effective Value Engineering
- Engage Multidisciplinary Teams – Successful VE requires input from various disciplines, including engineering, procurement, construction, operations, and maintenance. By involving stakeholders with diverse expertise, teams can generate well-rounded solutions that optimize functionality, cost, and performance.
- Start Early – The greatest cost-saving opportunities arise when VE is implemented during the early design and planning phases. Early VE integration allows for greater flexibility in design modifications without incurring significant rework costs. Conducting VE workshops during Front-End Loading (FEL) stages ensures that cost-effective alternatives are explored before detailed designs are finalized.
- Focus on Life Cycle Costs – Instead of merely evaluating initial capital expenditures, VE should consider the total cost of ownership, including operating costs, maintenance expenses, and end-of-life disposal. Using life cycle cost analysis (LCCA) ensures that decisions align with long-term project efficiency and sustainability goals.
- Document Decisions – VE recommendations should be well-documented to provide a clear rationale for proposed changes. Maintaining comprehensive records of function analyses, cost-benefit evaluations, and stakeholder discussions enhances transparency and facilitates future decision-making.
- Communicate Effectively – Stakeholder buy-in is critical for successful VE implementation. Teams should communicate the benefits of proposed changes through presentations, reports, and real-world case studies. Clear documentation of how VE solutions maintain or improve quality can help alleviate concerns and ensure alignment among all parties involved.
- Leverage Technology – Advanced digital tools such as Building Information Modeling (BIM), Artificial Intelligence (AI)-driven cost analysis, and cloud-based collaboration platforms enhance the efficiency and accuracy of VE studies. These technologies allow teams to rapidly model, compare, and visualize different design alternatives, streamlining decision-making and reducing analysis time.
By following these best practices, construction teams can maximize the benefits of value engineering, ensuring that projects achieve optimal cost-efficiency, sustainability, and long-term performance.
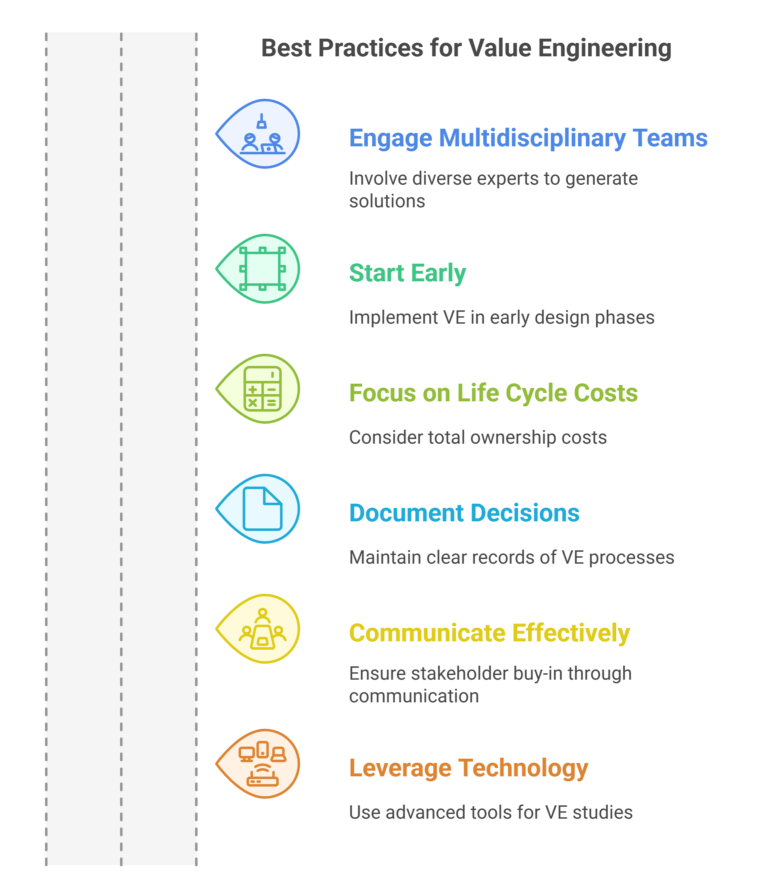
Conclusion
Value engineering is an indispensable process in modern construction projects. By prioritizing functionality, fostering collaboration, and encouraging innovation, VE enables cost efficiency, quality improvements, and sustainability. Its integration into the FEL process ensures that projects are developed with a focus on long-term value, aligning with budgetary and operational objectives.
Whether applied in material selection, energy efficiency enhancements, or construction methodology improvements, VE remains a cornerstone of effective project management. As the construction industry continues to evolve, leveraging advanced tools such as BIM, AI-driven cost analysis, and digital collaboration will further enhance the effectiveness of VE in delivering high-performance, cost-efficient, and sustainable projects.
Disclaimer
The information provided in this post is for reference purposes only and is intended to serve as a guide to highlight key topics, considerations, and best practices. It does not constitute professional advice or a substitute for consulting regarding specific projects or circumstances. Readers are encouraged to evaluate their unique project needs and seek tailored advice where necessary. Please Contact Us to discuss your particular project.