Pitfalls In Energy Project Estimating
Energy project estimating is one of the most critical components of project planning. A well-developed estimate provides the foundation for budgeting, decision-making, and project execution. However, even experienced estimators can fall into common traps that lead to cost overruns, schedule delays, and financial risk.
Whether you’re developing a conceptual estimate for feasibility studies or a detailed cost breakdown for project execution, understanding and mitigating estimating pitfalls is crucial. This article explores 10 of the biggest challenges in project estimating and provides actionable strategies to avoid them, ensuring your projects stay on time and on budget.
1. Underestimating Scope Complexity
The Problem:
One of the most frequent causes of inaccurate estimates is failure to fully define and understand the project scope. This can lead to:
- Missed cost elements due to incomplete design information.
- Unrealistic assumptions about project deliverables.
- Budget shortfalls requiring mid-project funding increases.
For example, a power plant project may initially estimate a certain number of heat exchangers but later realize additional units are needed due to process inefficiencies, leading to unexpected costs.
How to Avoid It:
✅ Use a progressive estimating approach (Class 5 to Class 1) to refine accuracy as the project matures.
✅ Conduct multidisciplinary scope reviews involving engineering, procurement, and construction teams.
✅ Leverage historical data from similar projects to validate scope completeness.
✅ Use detailed Work Breakdown Structures (WBS) to ensure all work packages are identified.
Real-World Example:
An oil refinery expansion project in the Gulf Coast underestimated the required piping infrastructure, leading to a 25% cost increase due to late-stage modifications. A proper WBS review could have identified this gap early.
2. Overlooking Risk and Contingency Planning
The Problem:
Many estimates either omit risk analysis entirely or apply generic contingencies (e.g., adding 10% without justification). This leads to either bloated or insufficient budgets.
For example, a project in a remote Arctic location may experience severe winter delays, yet the estimate fails to include contingencies for cold-weather productivity losses.
How to Avoid It:
✅ Use Monte Carlo simulations to model cost and schedule risks.
✅ Develop a risk register with quantifiable cost impacts.
✅ Categorize risks into quantifiable (e.g., price escalation) and qualitative (e.g., permitting delays) and assign proper contingencies.
Real-World Example:
A solar farm developer failed to account for interconnection delays with the local grid, causing a 12-month project delay and additional costs of $8 million.
3. Inaccurate Labor Productivity Assumptions
The Problem:
Many estimates rely on generic labor productivity rates without accounting for real-world conditions such as:
- Extreme weather.
- Union vs. non-union labor rules.
- Equipment access and material handling challenges.
A refinery shutdown project may assume 50 pipefitters can complete a task in 10 days, but field conditions reduce productivity by 30%, resulting in cost overruns.
How to Avoid It:
✅ Use historical project data specific to location and workforce conditions.
✅ Account for learning curves, shift differentials, and fatigue factors.
✅ Include weather-related productivity adjustments for seasonal or extreme climate projects.
Real-World Example:
A data center construction project in Las Vegas underestimated summer heat effects on worker productivity, leading to a 15% reduction in efficiency and an additional $3 million in labor costs.
4. Failing to Account for Market Volatility
The Problem:
Estimates often assume stable material pricing, ignoring factors such as:
- Commodity price swings (e.g., steel, copper, concrete).
- Global supply chain disruptions (e.g., COVID-19, tariffs, shipping delays).
- Local inflation and currency fluctuations.
A project estimating $5,000 per ton of structural steel may face sudden price hikes to $7,000 per ton, leading to massive budget shortfalls.
How to Avoid It:
✅ Use real-time supplier quotes rather than outdated pricing databases.
✅ Include escalation clauses for long-lead items.
✅ Work with procurement to establish bulk purchasing or hedging strategies.
Real-World Example:
An LNG terminal in Texas underestimated piping material costs, leading to a $50 million budget increase when global nickel prices surged.
5. Poor Integration Between Engineering and Estimating Teams
The Problem:
A lack of coordination between estimators, engineers, and procurement specialists often results in:
- Engineering choices that don’t align with cost assumptions.
- Last-minute design changes inflating costs.
- Procurement delays due to misaligned purchasing strategies.
How to Avoid It:
✅ Require early collaboration between estimating and engineering teams.
✅ Implement design-to-cost reviews to balance scope and budget.
✅ Use integrated estimating software for real-time data sharing.
6. Misjudging Indirect Costs and Overheads
The Problem:
Many estimates undervalue indirect costs, leading to major budget gaps. Common omissions include:
- Project management expenses.
- Site logistics and temporary facilities.
- Permitting and regulatory compliance.
- Financing, insurance, and legal costs.
These indirect costs, while not directly tied to materials or labor, significantly impact overall project budgets.
How to Avoid It:
✅ Develop detailed indirect cost models based on historical project data.
✅ Clearly distinguish between fixed overheads (e.g., corporate management costs) and variable project-specific costs.
✅ Include escalation factors for long-duration projects to account for inflation.
Real-World Example:
A major wind farm project failed to account for site logistics costs, including transportation of heavy turbine components to a remote location. The oversight led to an additional $12 million in unplanned costs.
7. Applying the Wrong Estimating Methodology
The Problem:
Using the wrong estimating method at different project phases can lead to significant inaccuracies:
- Bottom-up estimating too early → False precision.
- Parametric models without specific adjustments → Generic assumptions.
- Failure to adjust estimates over time → Misaligned cost expectations.
For instance, an industrial facility project used a highly detailed bottom-up estimate during feasibility stage before key design details were finalized. This led to multiple revisions and false confidence in early budget projections.
How to Avoid It:
✅ Use Class 5 estimates for early-stage planning and Class 1 estimates for final execution.
✅ Apply parametric estimating only when reliable benchmark data is available.
✅ Transition to bottom-up estimating once engineering is sufficiently complete.
Real-World Example:
An oil sands project relied on a parametric estimate based on outdated benchmarks, failing to account for increased labor costs in the region. This resulted in a $500 million cost escalation over two years.
8. Ignoring Lessons Learned from Past Projects
The Problem:
Many organizations fail to capture estimating lessons from past projects, leading to repeated mistakes in:
- Productivity assumptions.
- Procurement strategy.
- Material pricing trends.
- Risk factors and contingency planning.
Without a centralized knowledge base, estimators may unknowingly repeat previous errors.
How to Avoid It:
✅ Maintain a project estimating database with cost, productivity, and variance tracking.
✅ Conduct post-mortem analyses on completed projects.
✅ Standardize “Lessons Learned” meetings across projects.
Real-World Example:
A chemical processing facility experienced repeated cost overruns in estimating pipe installation. After a lessons-learned review, they adjusted productivity rates and installation factors, leading to a 10% cost improvement on future projects.
9. Underestimating Change Orders and Scope Creep
The Problem:
Many estimates fail to account for inevitable changes, leading to budget and schedule overruns. Causes include:
- Inadequate contingency for scope evolution.
- Lack of a structured change management process.
- Assuming the initial design will remain unchanged.
On large energy projects, design adjustments are common due to client preferences, regulatory approvals, or field conditions.
How to Avoid It:
✅ Include allowances for scope growth based on project complexity.
✅ Use a formal change management process to track, review, and price deviations.
✅ Establish a buffer in both schedule and budget to accommodate expected changes.
Real-World Example:
A refinery modernization project originally budgeted at $800 million saw costs exceed $1 billion due to scope additions that were not properly managed or estimated.
10. Lack of Estimate Validation and Peer Reviews
The Problem:
Estimates that aren’t independently reviewed often contain errors, leading to:
- Overlooked cost elements.
- Incorrect productivity assumptions.
- Inconsistent contingency application.
A lack of validation means errors go undetected until it’s too late to adjust project funding.
How to Avoid It:
✅ Implement independent estimate reviews by cross-functional teams.
✅ Use benchmarking tools to compare estimates against industry norms.
✅ Conduct regular estimate audits to ensure assumptions remain valid.
Real-World Example:
A large-scale petrochemical project avoided a potential $75 million overrun after a peer review identified a miscalculation in site mobilization costs.
Summary: Top Estimating Pitfalls and Solutions
Estimating Pitfall | Common Consequence | Recommended Solution |
---|---|---|
Underestimating Scope Complexity | Budget shortfalls and unexpected change orders | Use WBS and multidisciplinary scope reviews |
Overlooking Risk & Contingency Planning | Cost overruns due to unforeseen risks | Implement Monte Carlo simulations and structured risk analysis |
Inaccurate Labor Productivity Assumptions | Lower productivity and increased labor costs | Use historical productivity data and weather adjustments |
Failing to Account for Market Volatility | Material price fluctuations causing budget gaps | Utilize real-time supplier quotes and escalation clauses |
Poor Integration Between Engineering & Estimating | Misaligned cost assumptions and procurement delays | Encourage early collaboration between teams and shared project tools |
Misjudging Indirect Costs & Overheads | Significant budget gaps due to overlooked indirect costs | Develop detailed indirect cost models based on historical data |
Applying the Wrong Estimating Methodology | False precision or inaccurate cost assumptions | Match estimating methods to project phase (Class 5 to Class 1) |
Ignoring Lessons Learned | Repeating past mistakes and inaccurate projections | Maintain a central estimating database and conduct post-mortem analyses |
Underestimating Change Orders & Scope Creep | Constant budget increases and schedule delays | Account for expected scope growth and enforce change management |
Lack of Estimate Validation & Peer Reviews | Errors remain undetected, leading to major cost escalations | Conduct independent estimate reviews and use benchmarking tools |
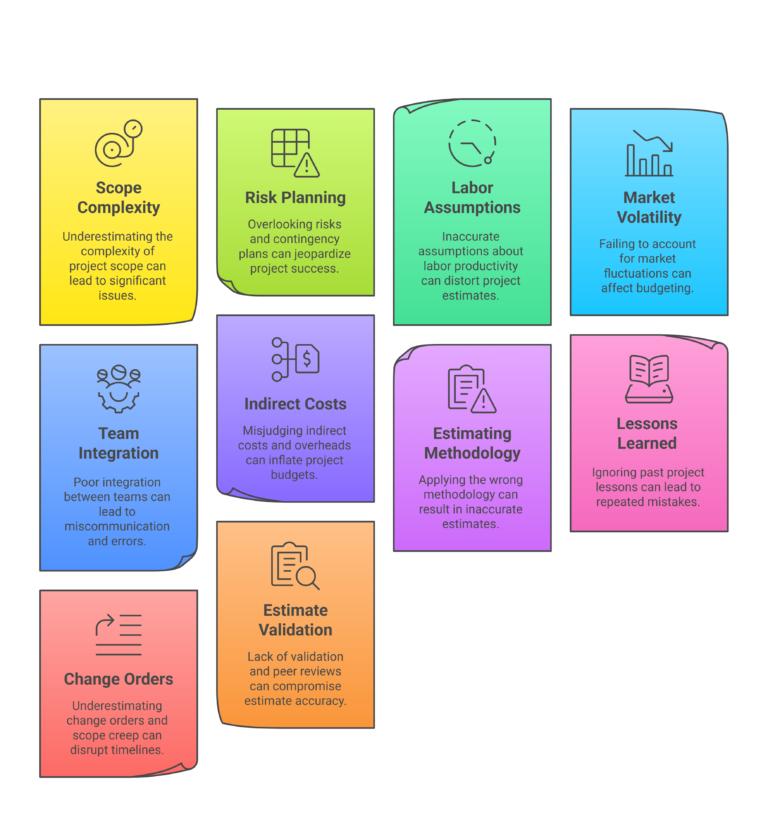
🔍 Case Study: LNG Terminal Project – Estimating Challenges & Lessons Learned
Background
A major energy company initiated a $1.2 billion liquefied natural gas (LNG) terminal on the U.S. Gulf Coast.
Estimating Challenges Encountered
- Missed regulatory compliance costs → $50 million cost overrun.
- Inaccurate labor productivity assumptions → 25% increase in labor costs.
- Material price surge → $120 million increase in steel and concrete costs.
- Hurricane season delays → Six-month delay without contingency planning.
Lessons Learned & Best Practices Implemented
✅ Enhanced scope reviews: Early involvement of regulatory experts.
✅ Risk-based estimating: Used Monte Carlo simulations to model cost escalations.
✅ Local labor market analysis: Factored in workforce availability.
✅ Procurement strategy improvements: Locked in steel and concrete prices early.
Turning Estimating Challenges into Strengths
Energy project estimating is inherently complex, requiring precision, adaptability, and proactive risk management. As highlighted in this guide, the most common estimating pitfalls, ranging from underestimating scope complexity to misjudging indirect costs, can lead to significant budget overruns, schedule delays, and financial risk.
By analyzing real-world case studies and historical data, we see that poor scope definition, overlooked risks, inaccurate labor productivity assumptions, and market volatility are among the most frequent estimating challenges. These issues often stem from insufficient collaboration, outdated methodologies, and a lack of structured contingency planning.
To mitigate these risks and improve estimating accuracy, project teams must adopt best practices such as:
✅ Progressive estimating approaches (Class 5 to Class 1) to refine accuracy over time.
✅ Advanced risk management techniques, including Monte Carlo simulations and structured contingency planning.
✅ Real-world labor productivity adjustments based on location, climate, and workforce conditions.
✅ Integration of procurement strategies to hedge against material cost fluctuations and supply chain disruptions.
✅ Robust collaboration between engineering, estimating, and project management teams to ensure alignment.
✅ Comprehensive post-mortem analysis of past projects to establish a reliable estimating knowledge base.
The key takeaway is that estimating should never be a one-time exercise. It must be a dynamic, data-driven process that evolves with project maturity. Organizations that proactively refine their estimating methodologies, leverage historical benchmarks, and integrate risk-informed decision-making will be better positioned to control costs, reduce uncertainty, and drive successful project execution.
By addressing these ten estimating pitfalls, project teams can transform estimating from a source of financial uncertainty into a strategic advantage, leading to fewer surprises, stronger cost predictability, and improved financial performance.
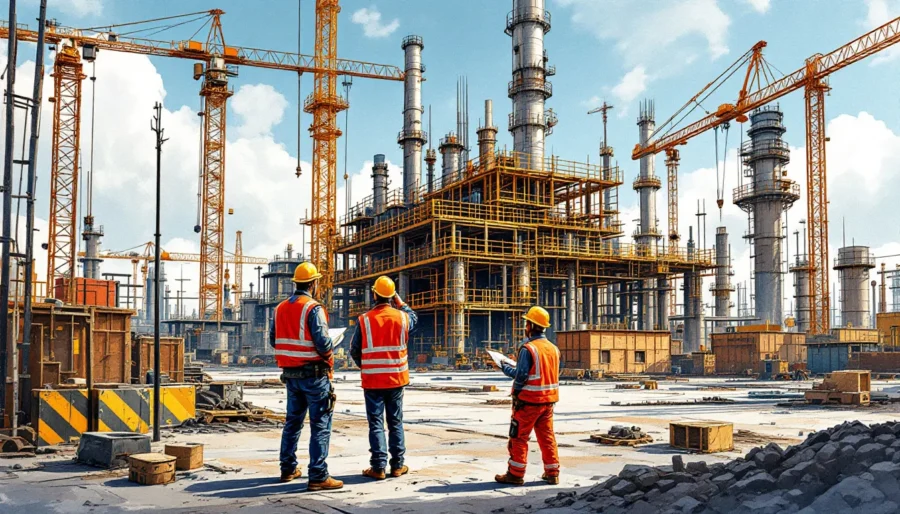
Disclaimer
The information provided in this post is for reference purposes only and is intended to serve as a guide to highlight key topics, considerations, and best practices. It does not constitute professional advice or a substitute for consulting regarding specific projects or circumstances. Readers are encouraged to evaluate their unique project needs and seek tailored advice where necessary. Please Contact Us to discuss your particular project.